1
/
of
1
PETIR388
PETIR388 >> AGEN SLOT GACOR DENGAN SCATTER HITAM TERBAIK SE-ASIA
PETIR388 >> AGEN SLOT GACOR DENGAN SCATTER HITAM TERBAIK SE-ASIA
Regular price
Rp 10,000 IDR
Regular price
Sale price
Rp 10,000 IDR
Unit price
/
per
Couldn't load pickup availability
PETIR388 merupakan situs slot gacor yang menyediakan fitur scatter hitam bonus terbaik saat ini yang sedang viral saat ini yang akan membuat kemenagan besar bagi anda para pemain slot gacor hari ini 2024.
Share
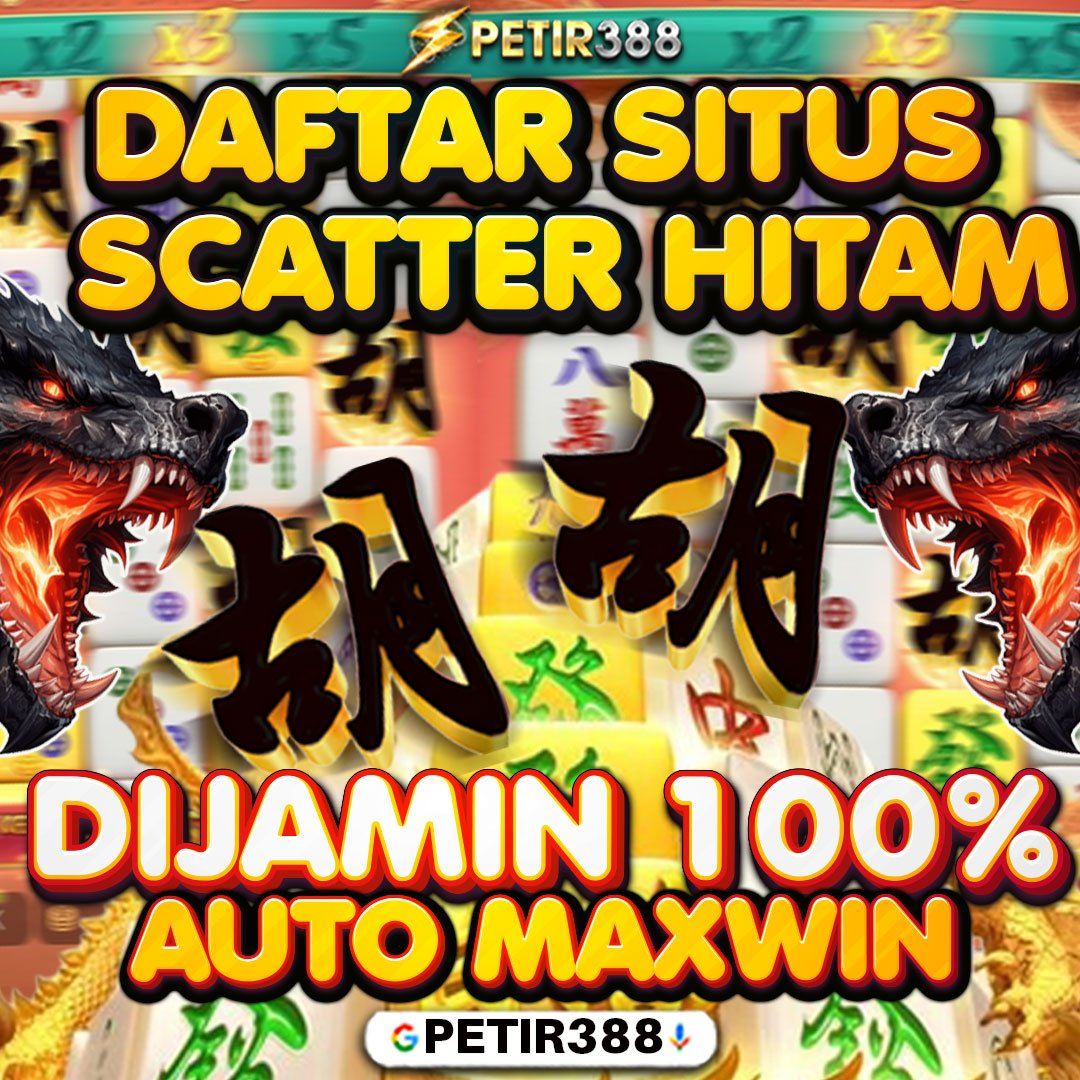